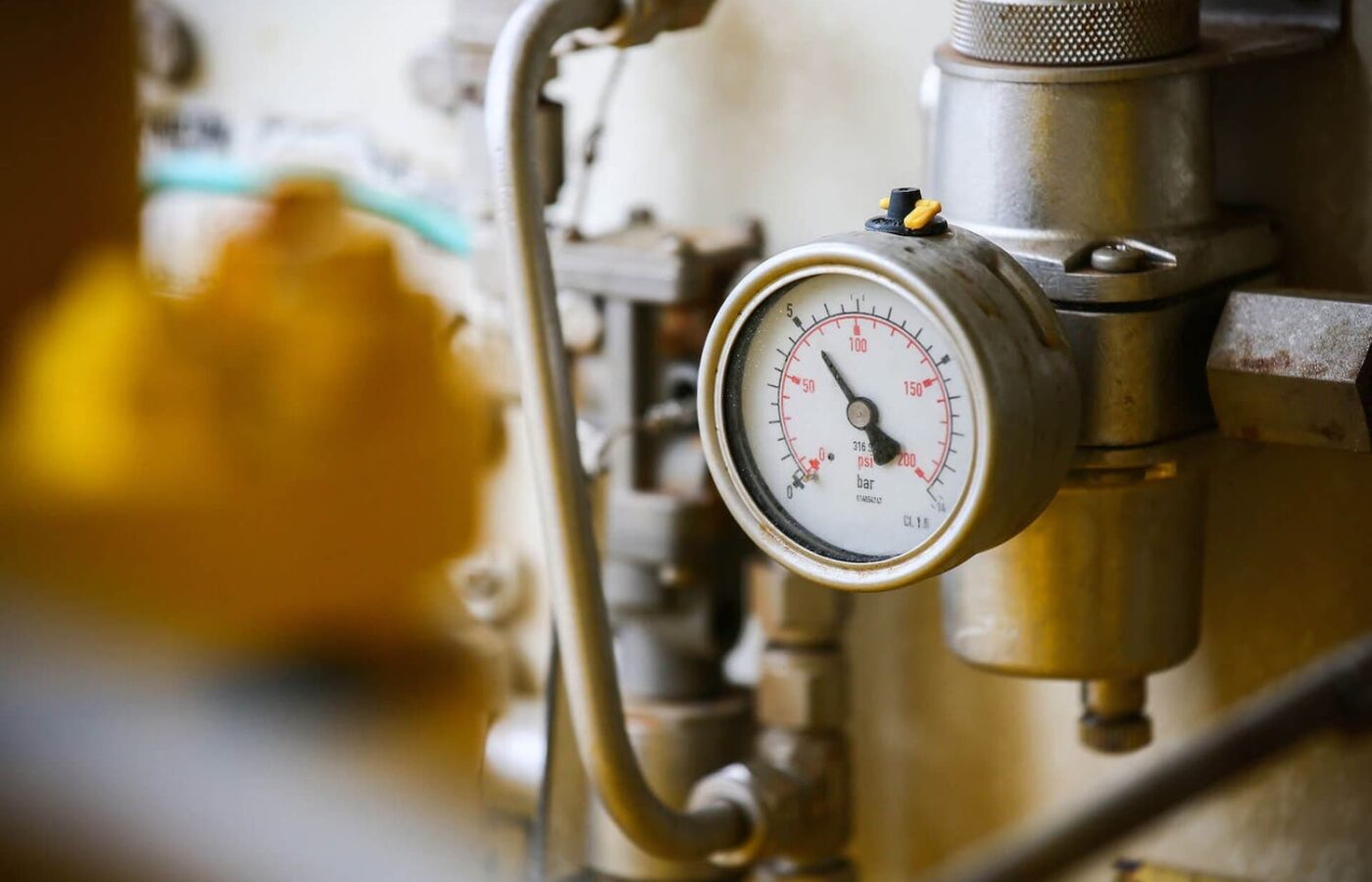
On-site Pressure calibrations:
Ideal for when your items can’t leave site or too bulky to send to us
On-site Pressure calibrations of:
The following items can be calibrated at your premises by our mobile calibration lab.
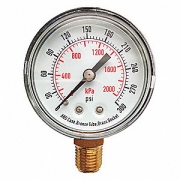
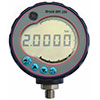
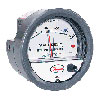
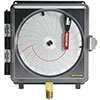
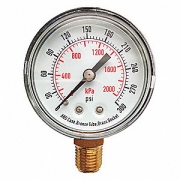
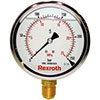
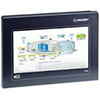
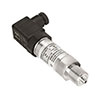
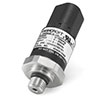
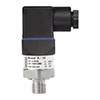
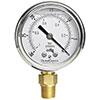
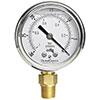
Benefits of having your equipment calibrated at your premises:
-
Minimal downtime
Our team of mobile technicians is like having your own on-site calibration facility. Assets can be calibrated and back in use quickly.
-
Same day calibrations
With our fully kitted out mobile team of technicians, we calibrate assets quickly, just metres from where they’re used
Book your calibration online now:
Speak to one of our experts to learn more about our calibration services
We Offer Expert Pressure Gauge Calibration:
With such frequent use and the assumed simplicity of the equipment, pressure gauges are often overlooked when it comes to maintenance.
To ensure they remain accurate, pressure gauges need to be calibrated at regular intervals, as using inaccurate equipment could lead to safety issues, production downtime or faulty products.
It is strongly advisable to calibrate pressure gauges once every 12 months. If left any longer, there is a possibility the equipment will drift out of specification, which would make the history of the instrument difficult to prove and may cause major production / process issues.
Electrical calibration service FAQ.
The answers to questions we get asked most frequently.
It is strongly advisable to calibrate pressure gauges once every 12 months. If left any longer, there is a possibility the equipment will drift out of specification, which would make the history of the instrument difficult to prove and may cause major production/ process issues.
For example, if an instrument was to drift out of calibration and it was last calibrated 24 months ago then all items processed using the data taken from the suspect pressure gauge will also be suspect and possibly need to be recalled. Whereas if the instrument was calibrated 12 months ago fewer suspect items may need to be recalled. Furthermore, the more calibrations performed on the instrument, the better the history the instrument will have giving greater uncertainty of measurements.
Calibration is also required when an instrument has been subjected to an unexpected shock or vibration that may have put it out of its specified limits. Between calibrations, if the pressure gauge has changed appearance, or if the dial or pointer has become cracked, blistered or has changed colour it may need to be sent out for an additional calibration.
Pressure gauge calibration can be performed through a variety of methods, including using a pneumatic/ hydraulic test pump (with an appropriately ranged and highly accurate reference gauge) or a pressure deadweight tester. Whichever option you choose should be carried out by experienced professionals using high quality, certified calibration equipment.
Using a suitable pressure media (gas or liquid), a test pump applies simultaneous pressure through the input ports found on either side of the pump, to the pressure gauge being tested as well as to a digital reference gauge. The readings on both are then compared to identify any discrepancies, this process is called calibration through comparison.
While a pressure deadweight tester (also known as a pressure balance) compares the pressure gauge being tested against a set of weights, taking into account a number of factors including gravity, buoyancy and revolutions per second – this type of calibration is often performed on pressure gauges where higher accuracy is needed.
After the test has taken place a calibration certificate must be provided with a record of the calibration results, including the calibration intervals and error limits, which should be kept to understand the instrument’s condition. No matter which calibration method is used, if any of the discrepancies are greater than the tolerance that has been defined, the pressure gauge will require an adjustment and re-calibration or to be taken out of service.
Pressure gauges are commonly used within a variety of industries and sectors. From processes as straightforward as inflating car tyres, all the way through to the complexities of manufacturing aerospace parts. However, with such frequent use and the assumed simplicity of the equipment, pressure gauges are often overlooked when it comes to maintenance.
To ensure they remain accurate, pressure gauges need to be calibrated at regular intervals, as using inaccurate equipment could lead to safety issues, production downtime or faulty products.
Replacement service:
If your electrical tester or instrument cannot be calibrated or is uneconomical to repair, we will contact you straight away and offer a branded like-for-like replacement. We will supply the replacement calibrated to your original order requirements.
Related Article: Why calibrate pressure gauges?
To ensure they remain accurate, pressure gauges need to be calibrated at regular intervals, as using inaccurate equipment could lead to safety issues, production downtime or faulty products.
Can’t see the items you need calibrating above?
We can calibrate much more than the items we’ve listed above, including pressure, temperature, torque, weight and mass equipment, so please drop us a message with your requirements and we’ll provide you with a quick, no-obligation quote.