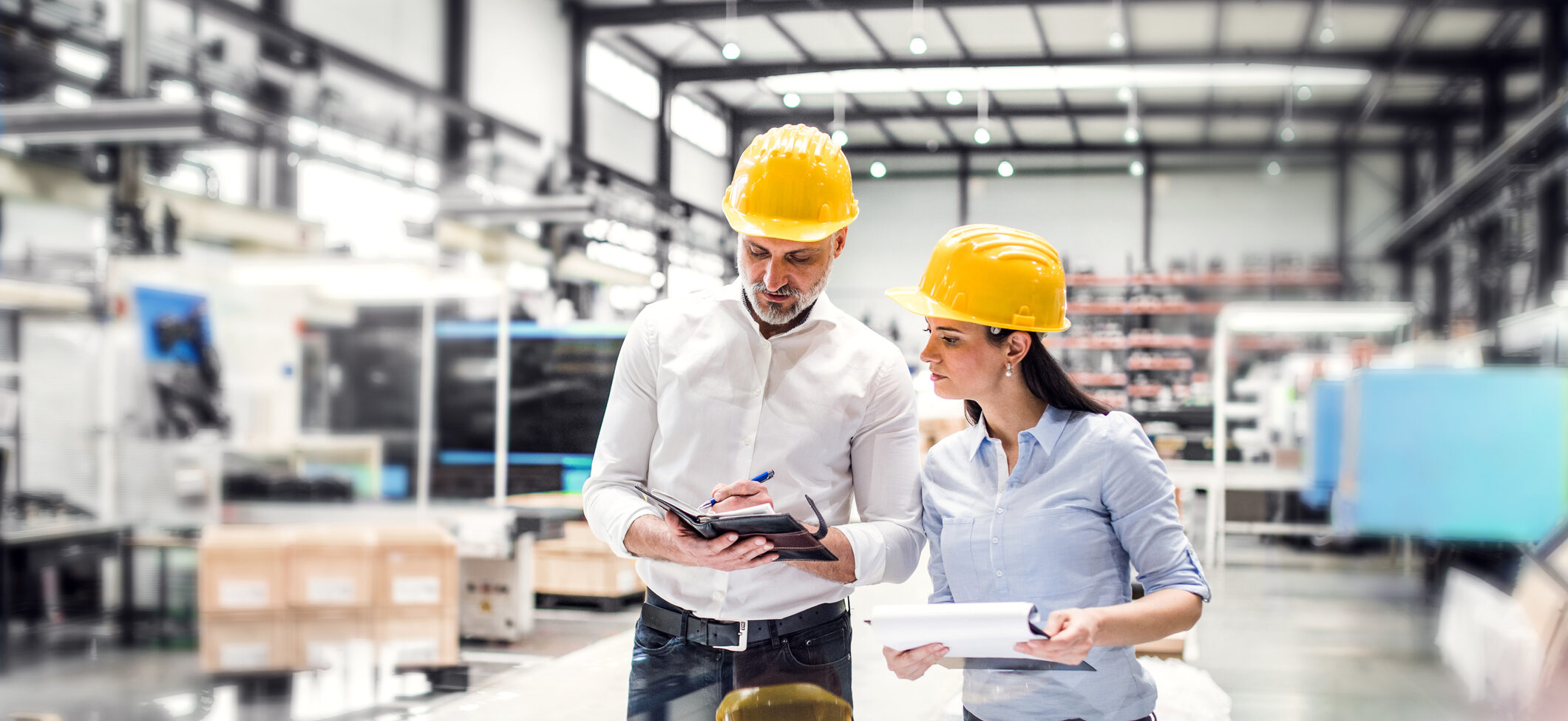
Top Three Tips for Audit-Compliant Calibration Certificates
22 February 2024
We’re open with all collection and drop off options operating as usual.
22 February 2024
22 February 2024
10 January 2024
2 March 2023
14 February 2023
15 July 2022
17 January 2022
14 December 2021
6 December 2021
8 November 2021