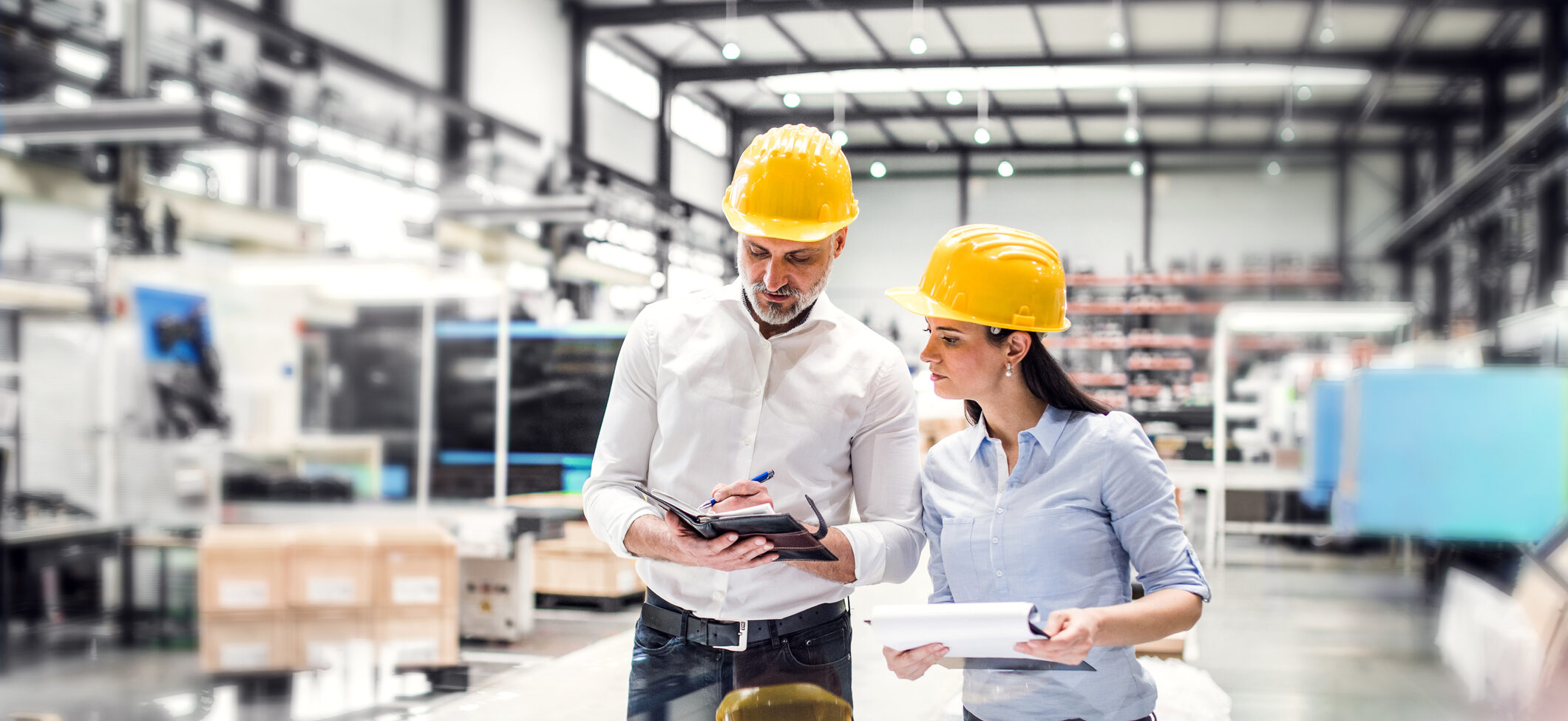
Top Three Tips for Audit-Compliant Calibration Certificates
22 February 2024
We’re open with all collection and drop off options operating as usual.
22 February 2024
14 February 2023
17 January 2022
14 December 2021
6 December 2021
8 November 2021
11 October 2021
30 September 2021
13 September 2021
1 September 2021